ProCam® Lab and ProCam® Compact expands product portfolio for camera production
TRIOPTICS expands its product portfolio in the field of active alignment of electronic camera modules and LiDAR systems.
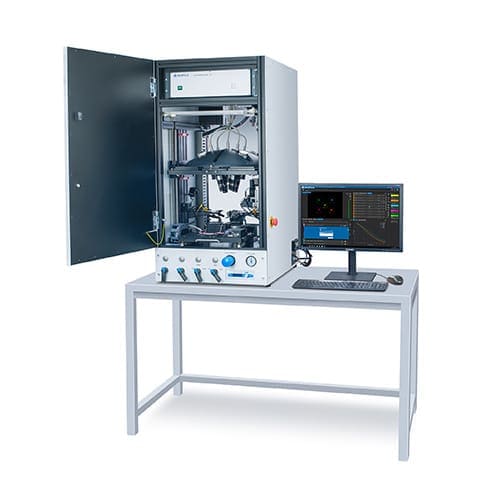
With ProCam® Lab and ProCam® Compact, TRIOPTICS is expanding its large product portfolio with two new systems for active alignment and production of camera and LiDAR modules. Thus TRIOPTICS meets the customer requirements regarding different production quantities and the special demands in the product life cycle of camera modules and LiDAR components.
ProCam® Lab for prototyping and small batches
ProCam® Lab is a newly designed system that meets the requirements of development tasks in the field of camera prototyping. The compact and modular design of the device enables flexible production of high-precision camera modules in small quantities. This system is mainly used in laboratories and is loaded manually. In addition to the ProCam® Lab basic unit, which includes a base frame with object generators, axes and integrated UV illumination for active alignment, customers can order a complete assembly line including a clean room cell and all necessary equipment and accessories for small batch production of camera modules.
“With this laboratory equipment from the ProCam® series, our customers can very quickly get started in the complex topic of active optical alignment. The measurements are done with highest precision and the proven TRIOPTICS measurement method, so that our customers work at the highest level right from the start. As production numbers increase, scaling up to mass production is now possible without changing technology,” explains Division Manager Dr. Dirk Seebaum.
ProCam® Compact for medium volumes and changing portfolio
The second new system of the product series is aimed at already established camera manufacturers. With the ProCam® Compact production system, TRIOPTICS offers an ideal solution for the challenge of the active alignment and production of camera modules at medium production volumes. The system is also suitable for frequent small production quantities that require quick configuration changes.
“The ProCam® Compact combines the precision of the TRIOPTICS process with the speed and reliability of a production machine such as our ProCam® TT. Focused on the essentials, the system ensures very accurate, repeatable and fast alignment and thus high image quality of the camera modules at mid-six-figure production volumes per year,” says Dr. Dirk Seebaum.
The ProCam® Compact system achieves a cycle time of 30 seconds per camera module. The cycle includes the process steps glue dispensing and glue bead inspection, active alignment, and UV-curing. The machine can be loaded and unloaded both manually and automatically and is also ideally suited to be integrated as a module in a camera production line.
Time and cost advantages thanks to adaptable processes
The ProCam® product group assists customers in all stages of production, from the laboratory to high-volume manufacturing, with a consistently high level of quality. All processes and sample-specific components – developed together with customers for alignment and production of the customized camera – can be adopted in later stages of production – from prototype production to small and medium series to large-scale production. This holistic support results in major cost benefits for customers and significantly reduces the time horizon for camera projects. Thanks to adaptable measurement and manufacturing processes, no more complex system changes are necessary when production volumes are scaled up.
ProCam® Lab for prototyping and small batches
ProCam® Lab is a newly designed system that meets the requirements of development tasks in the field of camera prototyping. The compact and modular design of the device enables flexible production of high-precision camera modules in small quantities. This system is mainly used in laboratories and is loaded manually. In addition to the ProCam® Lab basic unit, which includes a base frame with object generators, axes and integrated UV illumination for active alignment, customers can order a complete assembly line including a clean room cell and all necessary equipment and accessories for small batch production of camera modules.
“With this laboratory equipment from the ProCam® series, our customers can very quickly get started in the complex topic of active optical alignment. The measurements are done with highest precision and the proven TRIOPTICS measurement method, so that our customers work at the highest level right from the start. As production numbers increase, scaling up to mass production is now possible without changing technology,” explains Division Manager Dr. Dirk Seebaum.
ProCam® Compact for medium volumes and changing portfolio
The second new system of the product series is aimed at already established camera manufacturers. With the ProCam® Compact production system, TRIOPTICS offers an ideal solution for the challenge of the active alignment and production of camera modules at medium production volumes. The system is also suitable for frequent small production quantities that require quick configuration changes.
“The ProCam® Compact combines the precision of the TRIOPTICS process with the speed and reliability of a production machine such as our ProCam® TT. Focused on the essentials, the system ensures very accurate, repeatable and fast alignment and thus high image quality of the camera modules at mid-six-figure production volumes per year,” says Dr. Dirk Seebaum.
The ProCam® Compact system achieves a cycle time of 30 seconds per camera module. The cycle includes the process steps glue dispensing and glue bead inspection, active alignment, and UV-curing. The machine can be loaded and unloaded both manually and automatically and is also ideally suited to be integrated as a module in a camera production line.
Time and cost advantages thanks to adaptable processes
The ProCam® product group assists customers in all stages of production, from the laboratory to high-volume manufacturing, with a consistently high level of quality. All processes and sample-specific components – developed together with customers for alignment and production of the customized camera – can be adopted in later stages of production – from prototype production to small and medium series to large-scale production. This holistic support results in major cost benefits for customers and significantly reduces the time horizon for camera projects. Thanks to adaptable measurement and manufacturing processes, no more complex system changes are necessary when production volumes are scaled up.