TRIOPTICS introduces new lens feeding concept
With OptiCentric® Bonding 5D MultiAlign high-precision lenses can be produced with reduced mechanical complexity
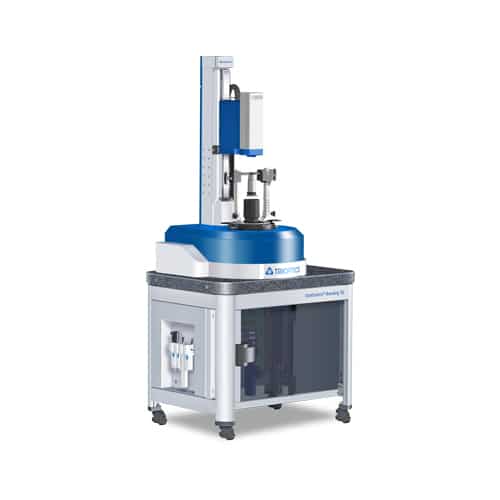
Until now, there has only been one way to manufacture high-precision optical systems and implement complex optical designs: the lens elements are precisely aligned in individual mounts and then assembled into a lens barrel. A new solution from TRIOPTICS now allows the alignment and bonding of multiple lens elements in five degrees of freedom directly into a single barrel. Based on the established OptiCentric® Bonding 5D alignment system, the new MultiAlign lens feeding concept is used to produce high-precision lenses with reduced mechanical complexity.
Development Engineer Christian Wilde explains: “The OptiCentric® Bonding 5D MultiAlign manufacturing process offers advantages in the optical design process. It allows the use of conventional lens designs without having to implement them as sub-cell designs. This reduces both the number and the requirements for mechanical fit tolerances. Compared to the sub-cell assembly, the design is therefore simplified.” With a centration measurement accuracy of 0.1 µm, the OptiCentric® Bonding 5D MultiAlign achieves alignment accuracies for each lens element of < 1 µm for centration and axial position and < 2 arc seconds for tilt.
The MultiAlign directional bonding concept can also reduce the weight and size of the lens. It further streamlines the manufacturing process. “The many small steps in the manufacturing process are eliminated,” says Wilde. “Instead of gluing the lens elements into their individual mounts before assembling them into a lens, everything is now done in one step. This saves manufacturing costs and time.” As with OptiCentric® Bonding 5D, this process is cleanroom-compatible.
Development Engineer Christian Wilde explains: “The OptiCentric® Bonding 5D MultiAlign manufacturing process offers advantages in the optical design process. It allows the use of conventional lens designs without having to implement them as sub-cell designs. This reduces both the number and the requirements for mechanical fit tolerances. Compared to the sub-cell assembly, the design is therefore simplified.” With a centration measurement accuracy of 0.1 µm, the OptiCentric® Bonding 5D MultiAlign achieves alignment accuracies for each lens element of < 1 µm for centration and axial position and < 2 arc seconds for tilt.
The MultiAlign directional bonding concept can also reduce the weight and size of the lens. It further streamlines the manufacturing process. “The many small steps in the manufacturing process are eliminated,” says Wilde. “Instead of gluing the lens elements into their individual mounts before assembling them into a lens, everything is now done in one step. This saves manufacturing costs and time.” As with OptiCentric® Bonding 5D, this process is cleanroom-compatible.